Control unit of XY & XYZ multi-axis robot
- Flexible combination applications allow single-axis robot to move linearly and realize 2D and 3D multi-axis motion functions.
- Diversified combination of modules provide customers with quick constructed machine units in different environments.
- Equipping with a 3-axis PTP servo controller without the cost of software development, we provide the standard man-machine interface or PC operating software, allowing you to complete one-stop shopping.
- MoCAT 3-axis controller is equipped with EtherCAT high-speed communication sDXFServo / AC / servo motor series.
1. EtherCAT Controller
|
Motion control
|
![]() |
Adapter board configuration

Hardware architecture
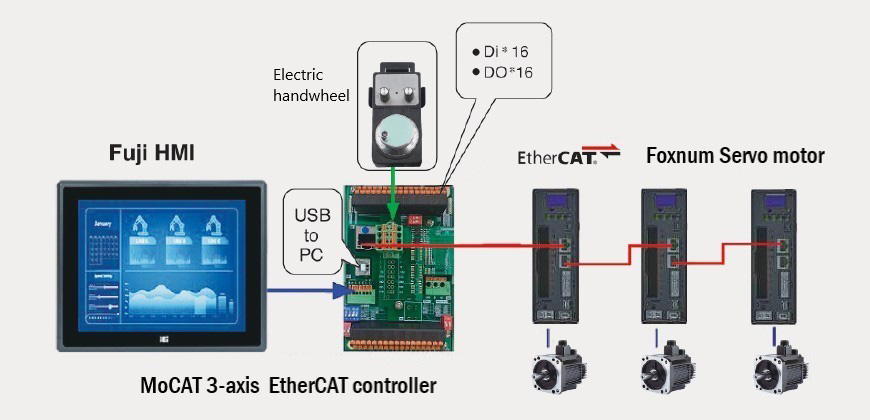
3-axis controller
3-axis robot
![]() The Y axis drives the X axis, and the X axis carries the workpiece. |
![]() The Y axis drives the Z axis, and the Z axis carries the workpiece. |
![]() The Y axis drives the X axis, and the X axis drives the Z axis to carry the workpiece, auxiliary axis supports on the side. |
![]() The X axis drives the Z axis horizontally, and the Z axis carries the workpiece. |
1. High performance
Auto-adjust
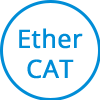
Automatically adjust parameters for specific mechanical structures to optimize system performance.
Vibration suppression
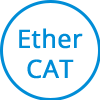
Provide 4 sets of notch filters and damping and vibration reduction functions.
It can automatically detect, suppress mechanical resonance, shorten overshoot and settling time with one button.
There is also a command filter function, which removes the frequency that will cause vibration of the end from the command end.
Two-degree-of-freedom feedforward control
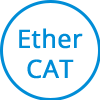
Independent feedforward control of speed and torque improves the position mismatch, so that there is no hysteresis between the output response of the system and the input command.
Command fine interpolation
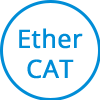
Improve the precision of position control and make the motor run more smoothly.
Friction compensation
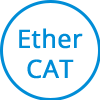
Compensate for the change of friction when the platform changes direction, and optimize the sharp angle error of the turning point of the action.
2. Multifunctional
Position/speedometer 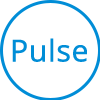
Multi-point control can be achieved without the controller sending pulses,, which saves the cost of using the pulse module. It can be used for multi-speed control and can also be used with controllers of different brands.
Position closed loop control
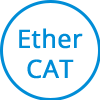
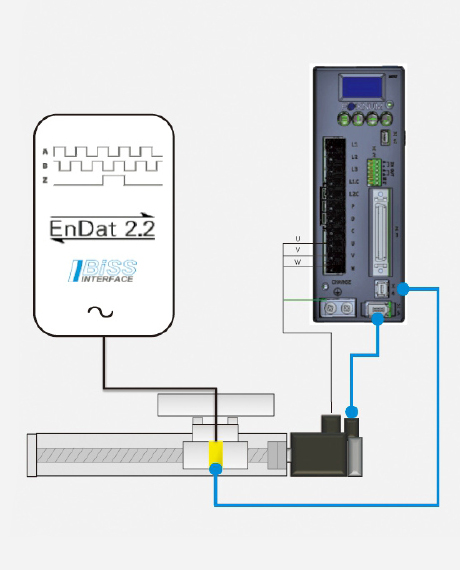
*To support the encoder, you need to select the corresponding driver model.
Digital torque limit 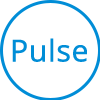
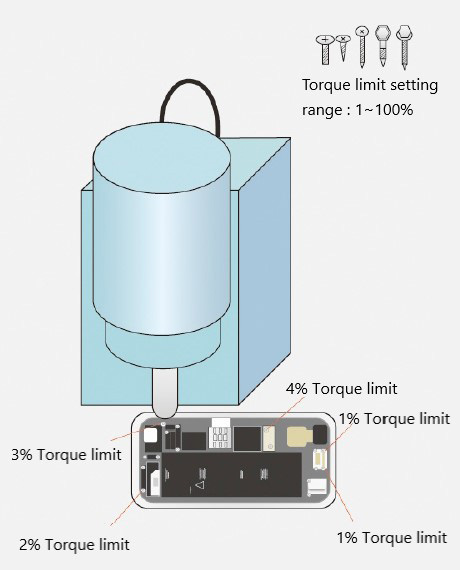
3. Flexible
Compatible with multiple types of motors
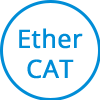
It can be used with multiple types of motors, such as permanent magnet synchronous motors, linear motors, direct drive motors, induction motors. Realize precise control of position, speed and torque, and support various applications of a single device.
4. Widely applicable
Widely used in automation industry equipment, CNC processing machines and specific machine equipment. 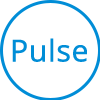
The FOXNUM servo driver (Pulse) series can expand digital IO up to 31 groups of programmable planning. The quantity of controllable tools depend on different control settings, up to 62 tools can be controlled.
The certain tool can be called and the positioning signal of the tool tray can be output for a specific coding method, or the specific function commands can be executed(Such as: first tool setting, emergency stop, offset automatic correction, etc.), and the different states of the tool magazine can be output(Such as: tool position offset, abnormal cylinder positioning alarm, etc.).It can be matched with various brands of controllers and systems.
![]() |
![]() |
![]() |
Digital IO control mode It can be applied to precise multi-point positioning, such as four-axis, tool magazine, indexing plate. For single-axis multi-point positioning or fixed stroke or angle indexing functions, this mode can save the use of motion control cards or pulse modules. |
Tool position compensation Write the indexing angle of the tool position into the encoder through the driver, so that the tool magazine will immediately store the indexing groups of the tool position in the encoder after assembling and calibrateing the tool position. So that after replacing the driver, there is no need to re-calibrate the position and re-set the indexing position of the tool. |
Offset automatic correction Allowable range of offset automatic correction operation. |
5. The Internet
Bus control 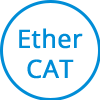
Support EtherCAT communication. Fast, simple wiring, can be applied to remote or distributed control requirements (in compliance with CoE)
High-resolution LCM display operation
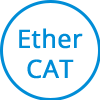
Dual frequency information monitoring, which can monitor commands and feedback at the same time, improving real-time debugging mobility, making it more user-friendly and closer to users.
Man-machine interface
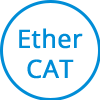
Graphical pages help customers quickly familiarize themselves with the software, setting parameters, monitoring the status of driver, executing performance adjustments and automatically adapting functions.
2. sDXF series servo driver
sDXF(Pulse) Automation equipment
The general purpose servo system is suitable for various automation equipment. It can be used with the supervisory controller of different brands, applied to equipment such as tools magazines, automated production lines, screw-locking machines, and handling robots. It can also support a variety of encoder feedback interfaces and fully closed loop controls. (Note: To support the encoder, you need to select the corresponding driver model)
sDXF(Pulse)-CNC/Machine tool
The bus-type servo system can shorten the cycle time of synchronous communication, and has advanced servo gain adjustment and multiple functions to realize high-precision and multi-axis simultaneous control, and meet the requirements of CNC, multiple axes or high simultaneous performance for machines and equipments. (Note: To support the encoder, you need to select the corresponding driver model)